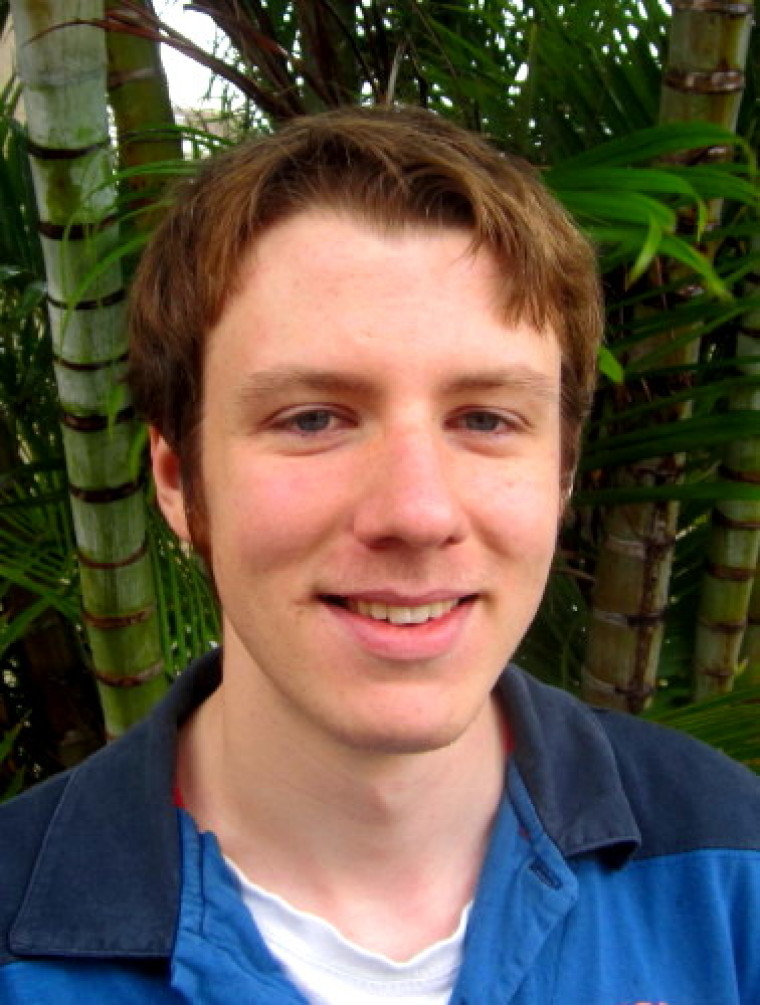
The Gear Stack Technique is a way of organising audio gear into three categories in order to keep equipment running for longer. It works by replacing old gear with new gear and then retiring the old to be repaired and reused at a later point in time.
Many venues don't have a strategy to do this because they have the money to buy new gear as well as replace equipment that died or has become outdated. Unfortunately for me at my church I haven't had that luxury; new equipment has only ever come in when a large portion of equipment dies, so it's necessary to keep a lot of equipment running with as little money as possible.
Audio equipment can be broken up into 3 different groups :
1. Fully Working/New
Gear in this group can be used and is gear that is used day to day and can afford to be manhandled when the technicians are not looking (Not advisable). Items such as mixers, amps, mics and speakers/monitors stay in this group for long periods of time because they don't get moved around a lot or have a strong structure. Not being dropped also helps keep gear here as well.
2. Behind the Scenes
Equipment in this group is used in spaces where the general public and performers don't see it or directly use it. Such equipment is generally old, had repairs and needs to be cared for when in use.
I often put repaired leads in this group; they work well but probably won't live up to the stress of being connected to a hand held dynamic mic or being trampled on and for those reasons they don't go back to the Fully Working group. The best place I find to place these leads are in highway runs and connecting equipment in the booth or other areas where there are no mindless performers that can damage the leads further.
I've also placed an old amp in this group after replacing the left channel potentiometer. The amp works but I have powered speakers now so it's not compatible with the current front of house configuration. It will however come in handy if I ever have a band and need an extra monitor and am short a powered wedge but have non-powered wedge lying around.
In short equipment here is generally gear that is used when you run out of equipment in the Fully Working group and need to fill in a space when you don't have enough good gear to do the configuration you want.
3. Waiting Repair/Modding
This is where gear goes to die. Equipment in this group is nonfunctional or semi-functional but has potential to be fixed, modified or reused in another project. In general I feel safe opening and exploring broken gear as it is already broken and not being used by anyone; so it's not going to matter if I make things worse.
I had a lot of XLR leads go here because they were bent from being connected to mics; people bend the first 1ft of the lead while talking, holding the mic, or incorrect storage rolling. Many XLR leads end up being moved into the Behind the Scenes group after I practice some soldering with some broken leads and some new connectors and thus the leads work again.
During the end of last year I had two mics pass into this group because they were both dead. I found them when I was going through some draws. In one the membrane cap had separated and in the other an internal wire had come away from a solder joint. The first one was fixed with a little electrical tape however the second one had more than just a loose wire problem and as such was not able to be fixed.
Not all equipment can be fixed sometimes equipment just dies and repairs are not feasible. I have only tried fixing analog audio equipment and I have a feeling that digital equipment possibly is a bit too complex to be fixing on my own. It would be better off being sent to a professional shop for fixing or just thrown out and replaced.
Wind Sock Washing:
If you take the head/basket off a mic you can remove the wind sock. Why remove the wind sock, you might ask? Well to wash it. I got around to actually doing that and let me tell you there was a lot of nasty stuff that came out. If you don't do it for 20 years; it's not a pretty sight. I've only been the audio guy at church for the last three years and there has always been something going on that prevents me from actually washing the wind socks. When I did Les Mis at school I washed 21 wind socks after every show and rehearsal to get rid of make-up that had rubbed into the wind socks.
Actually washing wind socks is quite easy. You carefully remove the wind sock from the rest of the mic and submerge the wind sock into some warm water, remove and leave to dry completely before you re-install the sock. It's a good idea to wash dynamic and headset wind socks every now and then to get rid of germs, spit and make-up.
Make-up generally stains wind socks of headsets, even if you wash them. However not washing them will mean the holes; in the sponge like substance the windsocks are made of, will clog up resulting in destroying or damaging the wind sock and it not preforming as designed (to reduce exhale breathing sounds).
Zach Radloff lives on the Gold Coast and is studying IT technology at university.
Zach Radloff's previous articles may be viewed at www.pressserviceinternational.org/zach-radloff.html